Trusted Sand Casting Supplier - Quality, Speed & Value
Leverage over 15 years of sand casting expertise to get high quality castings optimized for cost and delivery. We strategically balance automation with craftsmanship to provide an innovative, flexible, and cost-competitive platform for medium to high volume production.
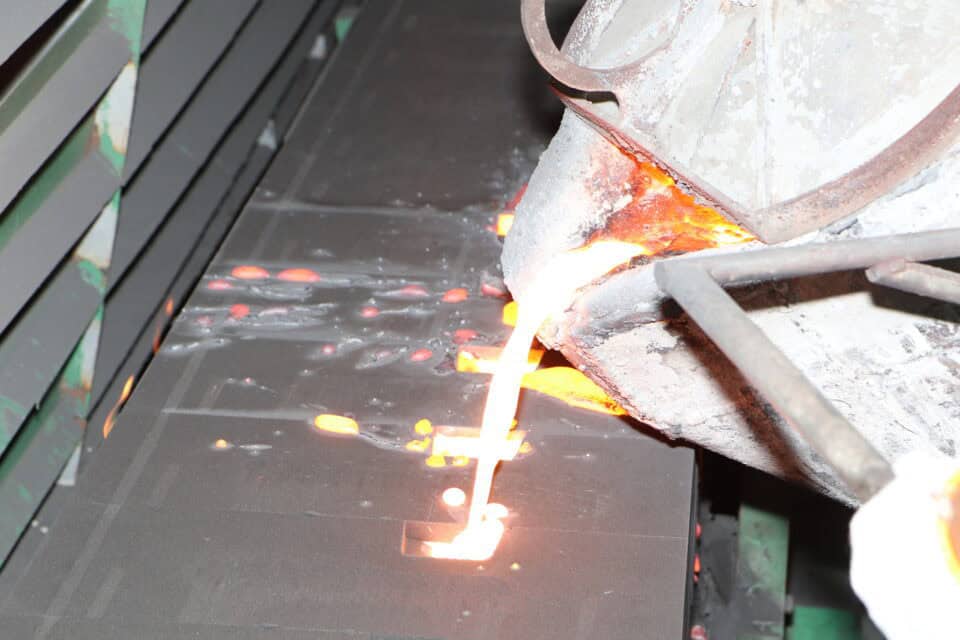
24h
Quick Quote±0.01
mm Tolerance30
days Mold Manufacturing20%
Purchase Cost Savings
Sand Casting Process
Sand casting is a cost-effective method for producing metal castings by pouring molten metal into sand molds. The sand, mixed with bonding agents, provides strength and shape retention. Chemically bonded sand is used for core assemblies, creating intricate internal structures.
To ensure proper permeability, the mold allows gas escape while resisting erosion. After solidification, castings are removed, and molds can be reused with reconditioning. Sand casting is versatile, suitable for small prototypes or high-volume production with various alloys.
We employ both green sand and chemically-bonded no-bake molds, ensuring flawless castings. Our engineers review designs before creating patterns, and molds are assembled before pouring liquid metal at precise temperatures. Additional services, such as CNC machining, heat treatment, and finishing, are also available.
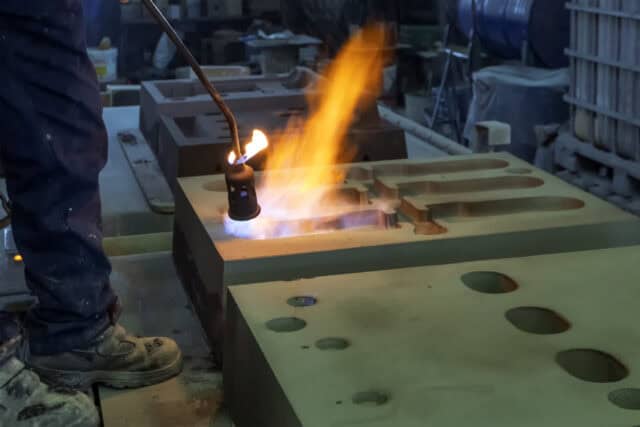
Service Features
Customized for Your Application
We provide high-quality sand castings at economical pricing coupled with best-in-class customer service.
Uncompromising Quality Management
Certified for ISO 9001 quality management standards, we perform over 35 stringent inspection checks for each process step using practices like x-ray, dye penetrant and CMM to ensure less than 0.1% defects.
Precision Molding Methods
We utilize a sophisticated heat-cured no-bake molding process, producing complex castings with exceptional surface finish and precision. This technique enables intricate contours, thin walls (down to 3mm), and RMS surface finishes up to 63 microinches.
Stringent Production Controls
We leverage stringent process controls and quality checks at each stage - including dimensional verification of patterns, molds and final castings against digital CAD models, we ensure tight tolerances and minimize variation order after order.
Get in Touch with Our Experts
- Respond to the request within 2 hours
- 30 days to complete the mold
- Sample production in 7 days
All uploads are secure and confidential
Sand Casting Variants
We offer a comprehensive range of sand mold casting processes including green sand, chemically-bonded no-bake, and investment sand casting.
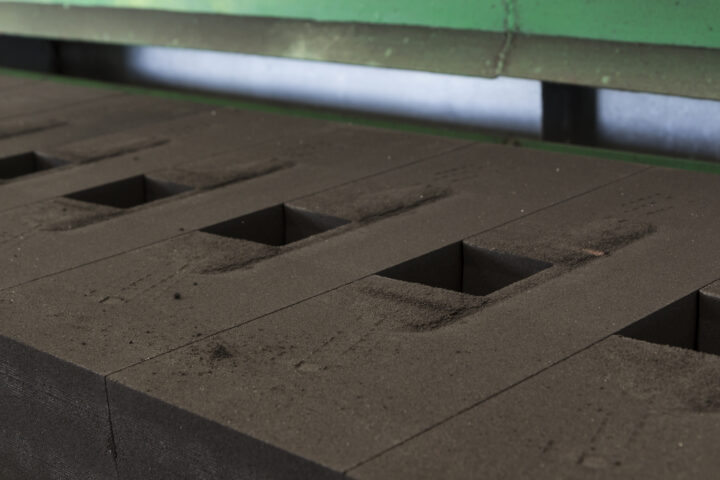
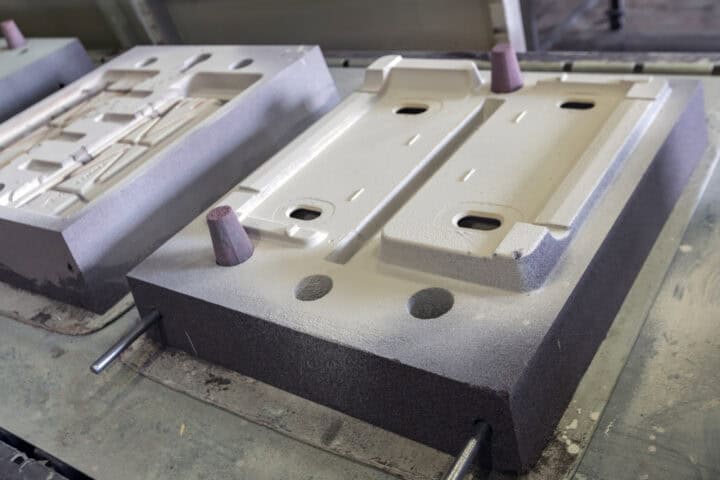
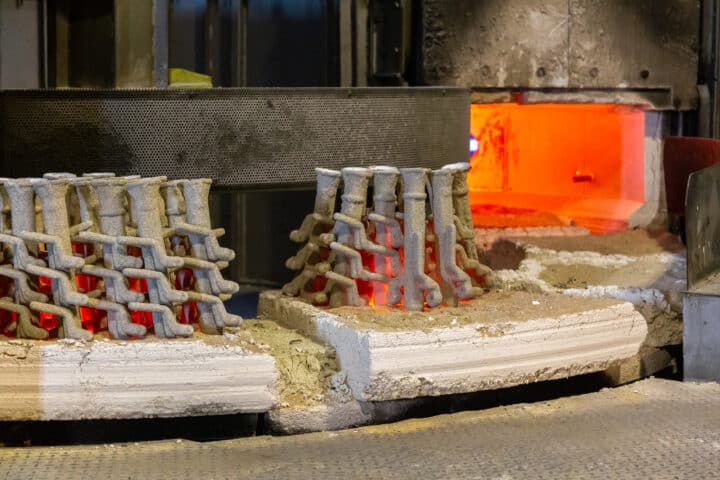
Sand Cast Metal Materials
- Stainless Steels
- Cast Iron
- Aluminum, Brass & Bronze
- Stainless Steels
- Cast Iron
- Aluminum, Brass & Bronze
- none
Customizable Surface Preparation and Machining
Sand Casting Finishes
We can prepare custom castings with over a dozen different finishing procedures to suit your product requirements - whether raw cast appearance, decorated surfaces, or precision machined features.
Name | Description |
---|---|
As Cast | The raw casting surface directly out of the mold can serve aesthetic or functional purposes like enhanced adhesion for coatings or friction effects for brakes. Available on most alloys. |
Abrasive Wheel Grinding | A consistent surface appearance or specification can be achieved through manual or automated abrasive wheel grinding whether finishing rough as-cast texture or removing excess. Various wheel specifications employed. |
Sand Blasting | High pressure air mixed with angular sand or glass beads produces distinctive impact dimple textures ideal for enhanced adhesion or decorative appearance prior to coating or plating. |
Glass Bead Blasting | A smoother low-gloss surface finish can be developed by abrasive blasting with spherical glass beads instead of sharper angular media. This provides a decorative finish or improved coating/bonding substrate. |
Chemical Etching | Submerging castings in acidic or caustic chemical baths produces specialized textures, exposes grain boundaries, and facilitates inspection which can serve functional or decorative roles. |
CNC Machining | complex geometries from a near net shape casting, we offer comprehensive in-house CNC machining including turning, milling, drilling along with manual operations like grinding, polishing, deburring and more. |
Get a Free Instant Quote
We will respond quickly to your needs within two hours and instantly customize a solution for you based on the information and drawings you provide.
Get Free Quote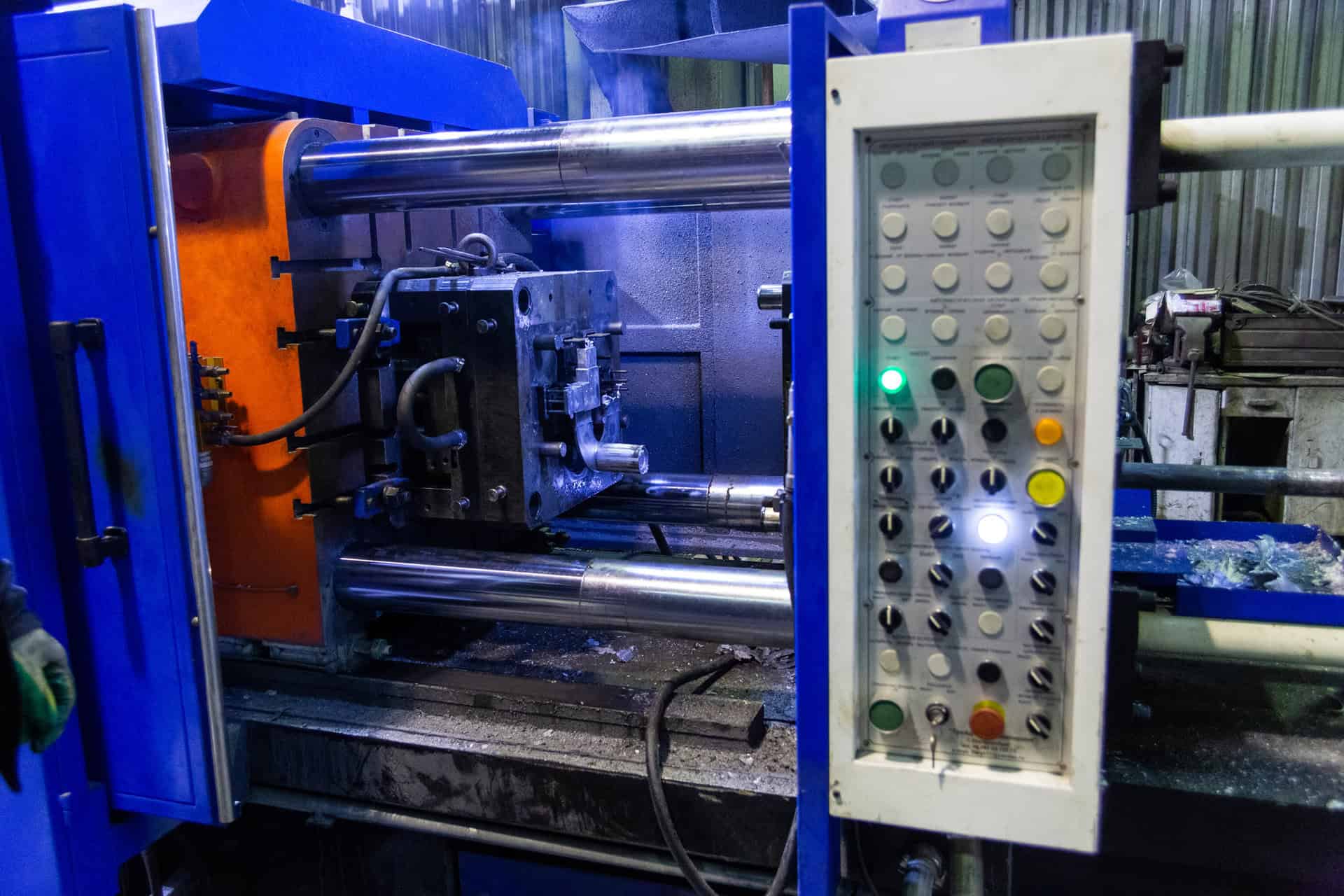
Applications of Sand Casting
Serving Diverse Sectors Through Custom Components
Our reliable, high-performance sand cast custom components improve products in manufacturing equipment, construction/agricultural machinery, automotive, medical, aerospace and more.
Advantages and Disadvantages
Quality Custom Castings at Competitive Cost
Sand casting offers a versatile production method to realize innovative metal parts in a wide range of weight sizes and complex geometries while providing competitive cost per part.
Disadvantages of Sand Casting
Disadvantages
Free Consultation- Higher per-piece cost vs other processes for volumes above 20,000 pieces.
- Not ideal for thin walls below 2mm for larger surface areas.
- Tighter tolerances below ±0.5% may require post-cast machining.
- Product consistency requires strict process control standards.
- Design changes require tooling adjustments.
Your Trusted Sand Casting Partner
Why Choose Us
Opt for precision, quality assurance, and flexible scalability with over 35 checks. Collaborate with us for seamless customer partnership and benefit from our continuous improvement culture.
Precision Engineering
Our engineering team leverages extensive foundry expertise to optimize designs and conduct in-depth process analysis using quality engineering tools for reduced variation and defects. We perform over 35 stringent checks to ensure excellence.
Flexible Scalable Capacity
With a vast range of tooling and production assets, we can seamlessly scale capacity and lead times to meet demand whether you require 1 piece or 1,000,000 pieces. We grow our capabilities alongside customer needs.
Customer Collaboration
We thrive on co-development partnerships with clients by encouraging collaboration across the product life cycle - from initial concepts to refinement to long term supply. Our success stems from shared success.
Continuous Improvement
We continually challenge ourselves across technology, quality, delivery, and service metrics through lean initiatives to maximize customer value. Our highly skilled workforce makes this possible through expertise, teamwork and commitment.
Frequently Asked Questions
See below for common sand casting questions and answers, or contact us if you have additional questions!
What Are Your Typical Lead Times?
What Size Ranges Can You Produce?
Can You Manufacture Directly From My 3D CAD Model?
What Are Your Minimum Order Quantities?
What Type of Post-Casting Finishing Do You Offer?
Where are you located? Can I visit?
Get a Free Instant Quote Now
Contact Us Today
Our experts are online 24h, will respond quickly within two hours of receiving your demand, and immediately customize personalized one-stop solutions for you according to the information and drawings you provide.
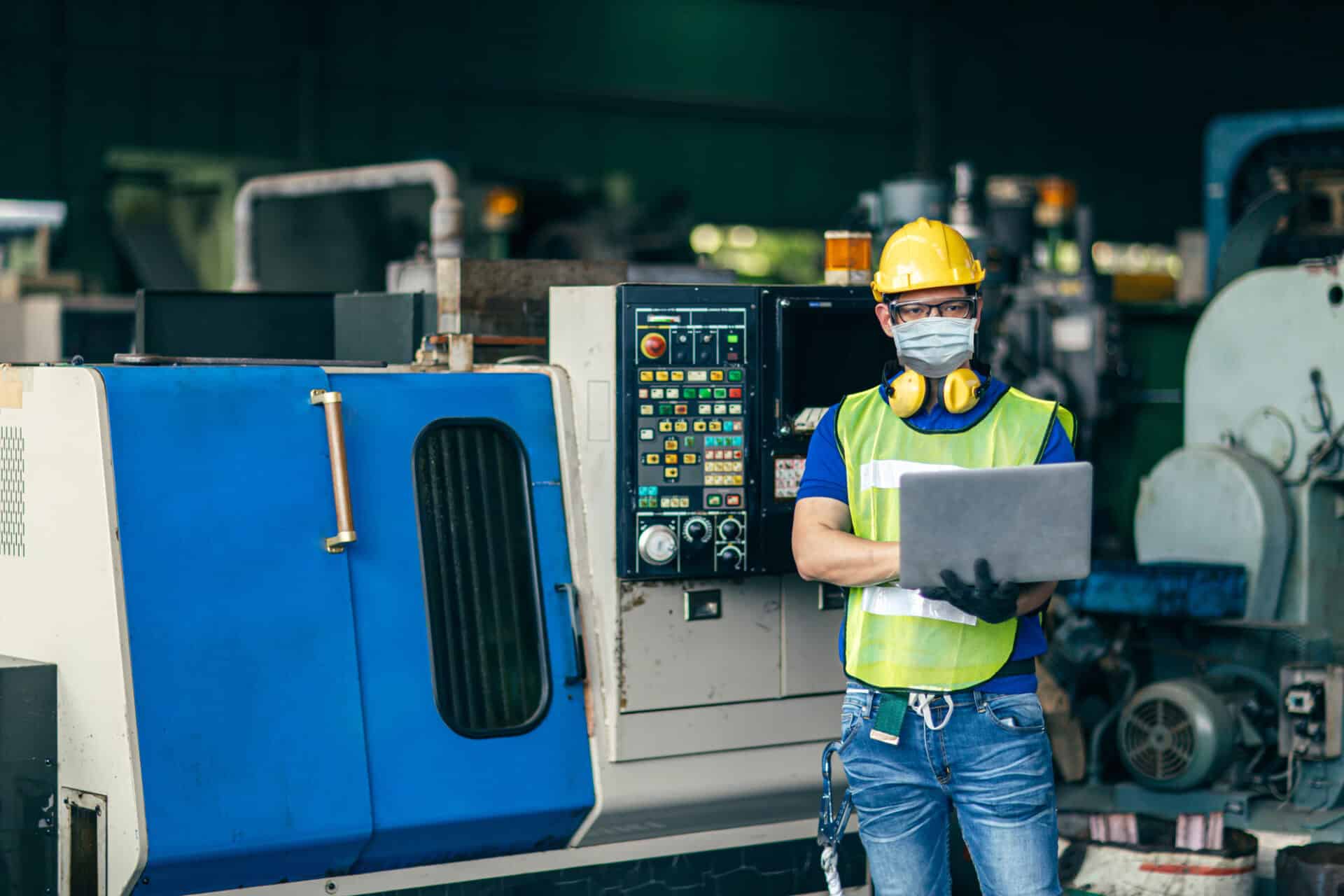