Your One-Stop Solution for Aerospace Parts and Prototypes
With over 10 years of experience serving the aerospace industry, we provide end-to-end services from design to delivery of custom prototypes and parts production. Partner with us for expert advice and manufacturing excellence.
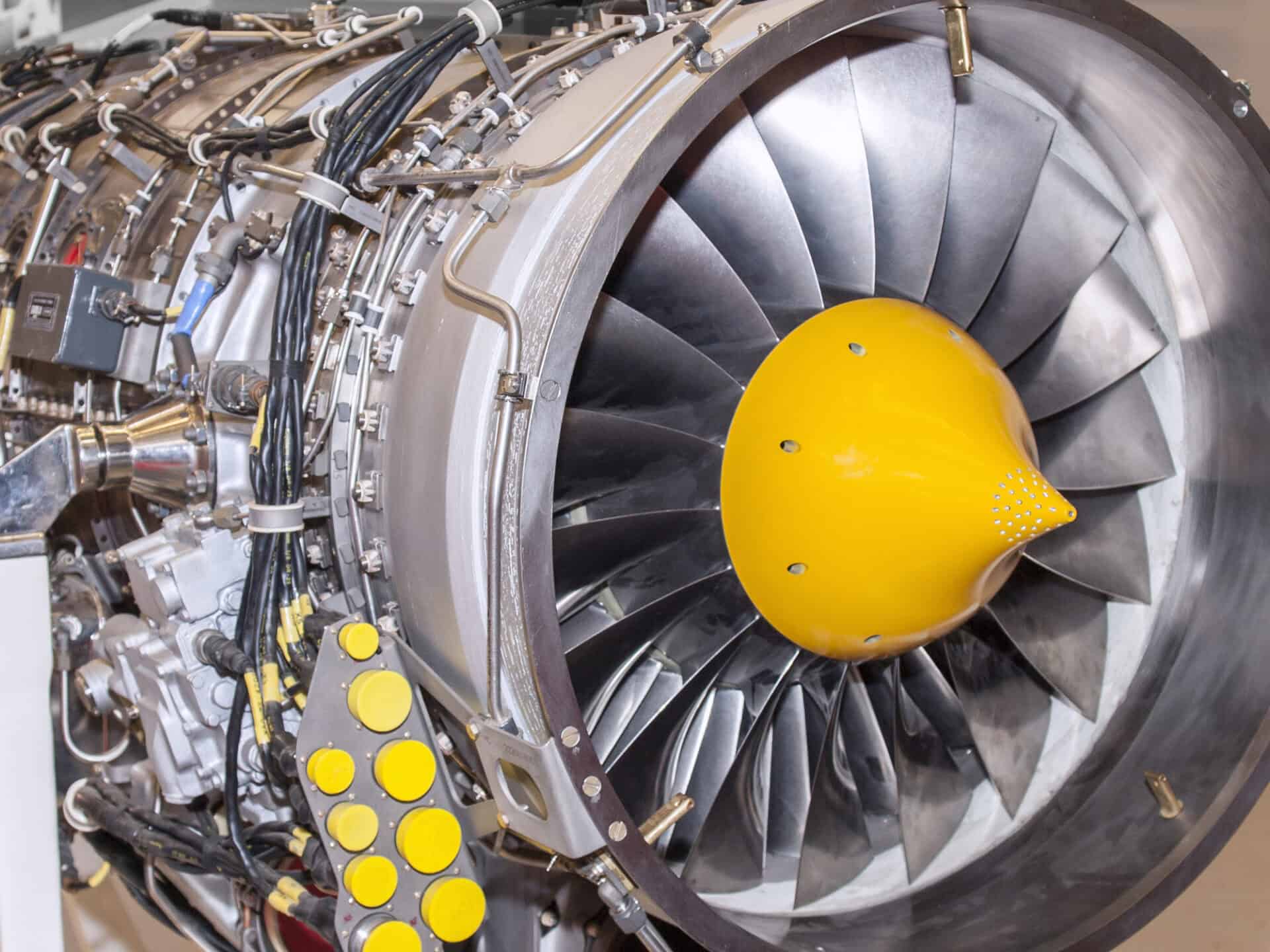
Why Partner With Us?
Driven by Quality, Focused on Innovation
By investing in advanced technologies and skills enhancement, we deliver high-precision aerospace components on schedule.
Iterative Design Refinement
We help refine component designs through rapid prototyping techniques leveraging 3D printing and CNC machining. Multiple design iterations are tested against engineering feasibility, conformance to specifications, manufacturability, and other parameters. Suggestions for design optimization reduces development time and costs.
Fully Integrated Production Systems
Our expansive facility houses interconnected systems for each manufacturing and finishing process - CNC machining centres, casting stations, heat treatment furnaces, surface treatment areas etc. This enables seamless production as per predefined stages, minimizing transfer time between steps.
Extensive Material Inventory
We maintain a vast and expanding inventory of certified aerospace-grade raw materials to manufacture components precisely according to customer specifications. Our sourcing team closely monitors regulatory updates to ensure all materials comply with the latest aviation industry standards.
Step-by-Step Aerospace Manufacturing Process
We optimize every operation in the prototyping and production cycle through expertise and smart integration of advanced technologies.
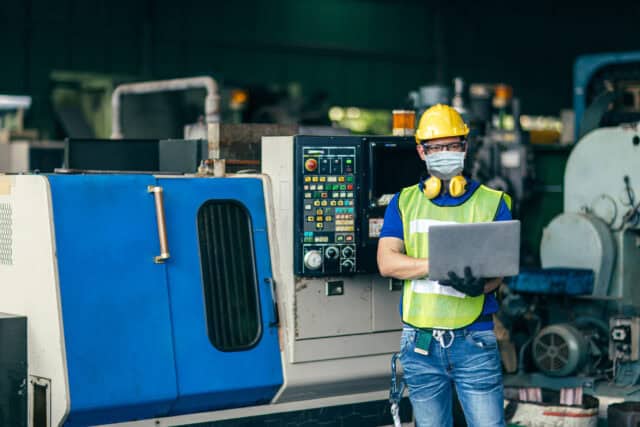
Design Optimization
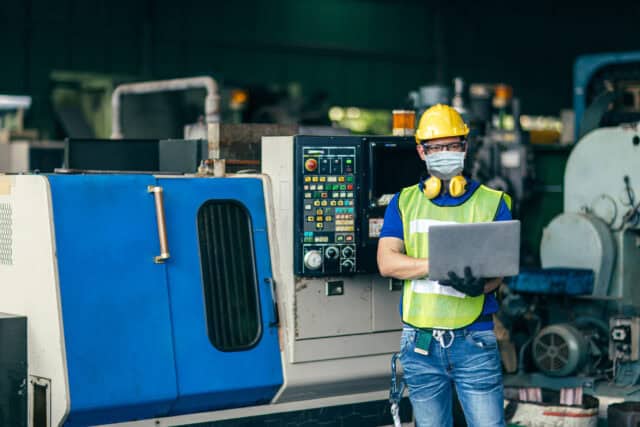
Raw Material Procurement
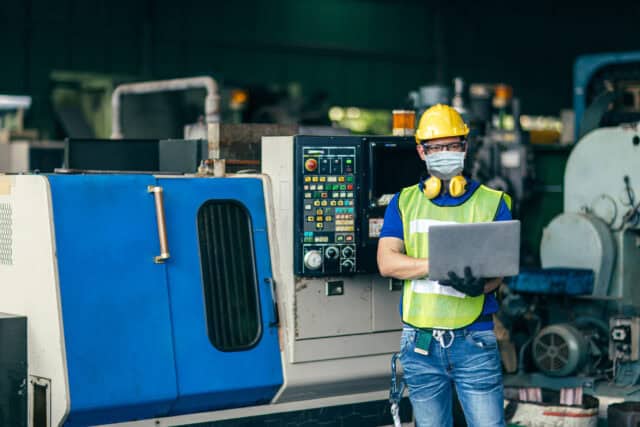
Precision Manufacturing
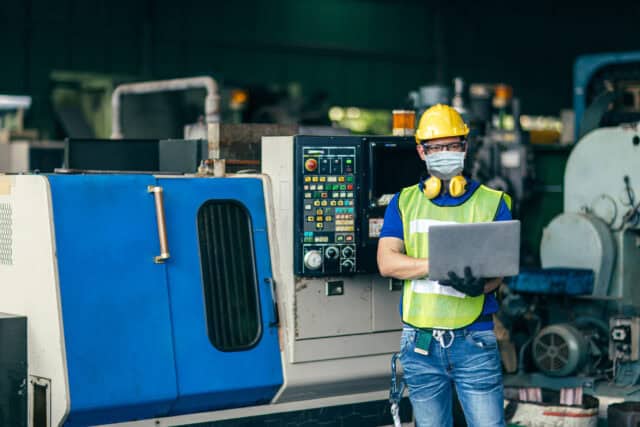
Quality Testing and Certification
End-to-End Aerospace Production for Zero Defects
By seamlessly integrating precision technologies with skilled craftsmanship, we ensure strict adherence to custom aerospace specifications right from raw materials through to final delivery.
Precision CNC Machining
Our CNC machining facility is equipped with over 50 high-performance 5-axis mills and lathes to handle large aerospace part production. The machines can manufacture parts from difficult-to-machine alloys like titanium, hastelloy, waspaloy etc.
while holding micron-level dimensional tolerances and surface finish under Ra 0.4μm. Our expert programmers and machinists ensure efficient metal removal and defect-free machined components.Investment Casting Foundry
The investment casting foundry provides a reliable production route for complex and thin-walled aerospace castings. Using the lost wax process, we create intricate ceramic moulds to be filled with molten aerospace alloys like nickel, steel or titanium based grades. The cast parts feature excellent surface finish and dimensional accuracy. Post-cast heat treatment and HIP processes deliver enhanced mechanical properties.
Advanced Finishing and Inspection
To meet exacting aerospace surface requirements, parts undergo treatments such as anodizing, shot peening, passivation etc. using automated systems for repeatability. We also operate one of the largest private metallurgical labs to validate composition, microstructure and mechanical properties through standardized testing methods. The in-house capabilities assure customers of part quality prior to shipment.
Send Your Request to Our Experts
Get in touch with our experts to analyze your project and customize an exclusive solution.
Send Email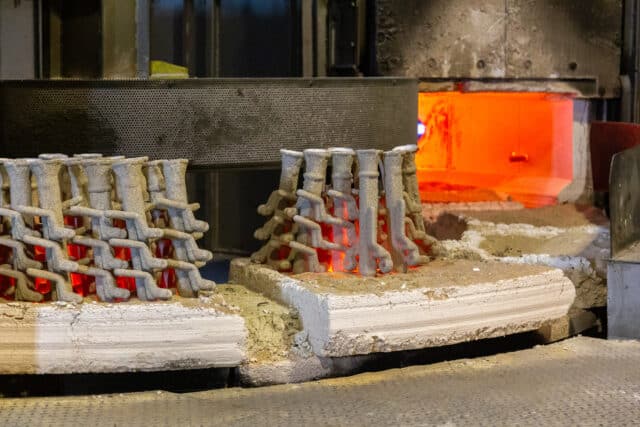
Extensive Range of Advanced Aerospace Materials
- Aluminum Alloys
- Aluminum Alloys
Surface Treatment of Aerospace Parts
Image | Name | Description |
|
Hard Anodizing | Anodizing develops a hard ceramic aluminum oxide layer up to 0.1mm thick for markedly improved wear and abrasion resistance. We use chromic acid processes suited for tight-tolerance aerospace components. |
|
Thermal Spray Coatings | Wear/fretting resistant coatings like WC-Co can be thermally sprayed on landing gear and other assemblies seeing repetitive friction and adhesion. Other coatings include solid film lubricants and NDT penetrant indication aids. |
|
Chemical Conversion Coatings | Iridite and alodine processes chemically develop protective surface films on aluminum alloys for corrosion inhibition and improved paint adhesion. Widely used as a pre-treatment before primer application. |
|
Plating | Electroless nickel with good ductility and corrosion resistance is widely used as an undercoat for subsequent chroming or wear resistant PTFE-based top coats. Decorative plating in gold, silver is offered for executive aircraft furniture. |
|
Paint Finishing | UV and corrosion resistant polyurethane topcoats specially formulated for aerospace require compatible chemical conversion coating and epoxy primers. Infrared reflective exterior coatings can manipulate radiation heat transfer. |
|
Laser Marking | Our high contrast laser marking process provides permanent, non-contact identification marking or logos resistant to operating environments. Widely preferred over fragile engraved nameplates. |
.wpDataTables.wpDataTablesWrapper.wdtVerticalScroll { overflow-y:auto; height:600px; }
.wpDataTableContainerSimpleTable .wdt-res-wrapper.active {overflow: initial; max-height:600px !important; }
.wpdt-fs-000018 { font-size: 18px !important;}
.wpdt-fs-000014 { font-size: 14px !important;}
/* th background color */
.wpdt-c.wpDataTablesWrapper table.wpdtSimpleTable.bt[data-has-header=’1′] td.wpdt-header-classes,
.wpdt-c.wpDataTablesWrapper table.wpdtSimpleTable thead th,
.wpdt-c .wpDataTablesWrapper table.wpDataTable thead th,
.wpdt-c .wpDataTablesWrapper table.wpDataTable thead th.sorting {
background-color: #000000 !important;
background-image: none !important;
}
Name | Description |
---|---|
Hard Anodizing | Anodizing develops a hard ceramic aluminum oxide layer up to 0.1mm thick for markedly improved wear and abrasion resistance. We use chromic acid processes suited for tight-tolerance aerospace components. |
Thermal Spray Coatings | Wear/fretting resistant coatings like WC-Co can be thermally sprayed on landing gear and other assemblies seeing repetitive friction and adhesion. Other coatings include solid film lubricants and NDT penetrant indication aids. |
Chemical Conversion Coatings | Iridite and alodine processes chemically develop protective surface films on aluminum alloys for corrosion inhibition and improved paint adhesion. Widely used as a pre-treatment before primer application. |
Plating | Electroless nickel with good ductility and corrosion resistance is widely used as an undercoat for subsequent chroming or wear resistant PTFE-based top coats. Decorative plating in gold, silver is offered for executive aircraft furniture. |
Paint Finishing | UV and corrosion resistant polyurethane topcoats specially formulated for aerospace require compatible chemical conversion coating and epoxy primers. Infrared reflective exterior coatings can manipulate radiation heat transfer. |
Laser Marking | Our high contrast laser marking process provides permanent, non-contact identification marking or logos resistant to operating environments. Widely preferred over fragile engraved nameplates. |
Trusted for Critical Aerospace Hardware
We manufacture intricate prototypes and parts deployed across aircraft systems and space applications.
Critical Airframe and Fuselage Structures
Sophisticated Flight Control and Avionics Parts
Safety-Critical Engines and Landing Gear Parts
accent heading
Call to action heading
- A great selling point goes here
- A great selling point goes here
- A great selling point goes here
These are the terms of the opt-in form.
Explore Our Aerospace Parts
Our Product Cases
View a small sampling of the critical aerospace parts we have manufactured. Contact us to know more.
Explore More Industries We Support
While aerospace forms a major share of our business, we leverage the same advanced manufacturing competencies to cater to critical components across energy, medical, industrial and automotive domains.
Construction
Leveraging expertise on robust design, we manufacture heavy equipment components including powertrain parts, hydraulics, attachments, undercarriages etc. for reliability in punishing operating conditions.
Medical
We offer specialized investment casting, machining and finishing capabilities for hip/knee implants, surgical instruments featuring biocompatible alloys fulfilling stringent medical device protocols.
Automotive
We produce engine components (pistons, valves etc.), drivetrain parts (gears, shafts, bearings), chassis assemblies (links, stabilizers) as well as panel fasteners for passenger and commercial on-highway vehicles.
Agriculture
We possess expertise to produce metal parts for tractors and harvesting combines including hitch categories, hay tools, planting and tillage equipment, precision farming machinery etc. This covers cast and fabricated chassis, gearbox housings etc.
Guides on Manufacturing
Access more information on our manufacturing capabilities through white papers, ebooks and blog posts.
Get a Free Instant Quote Now
Contact Us Today
Our experts are online 24h, will respond quickly within two hours of receiving your demand, and immediately customize personalized one-stop solutions for you according to the information and drawings you provide.
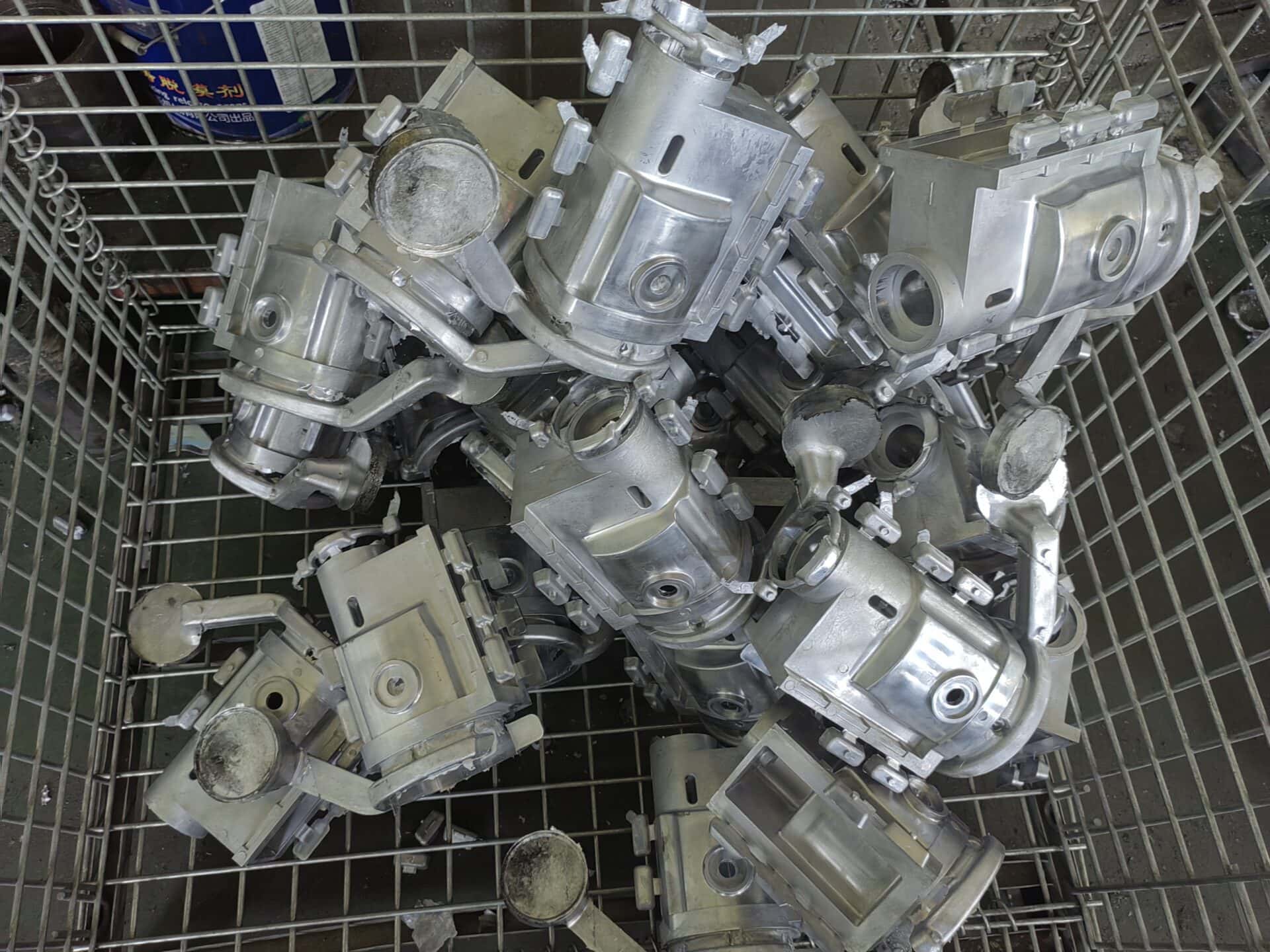