One-Stop Custom Die Casting Services
As a leading die casting manufacturer with over 10 years of experience, we provide a comprehensive range of die casting capabilities to produce complex, high-quality metal components. With in-house expertise across the entire die casting process, we partner with you to understand your product needs and deliver customized solutions that bring your visions to life.
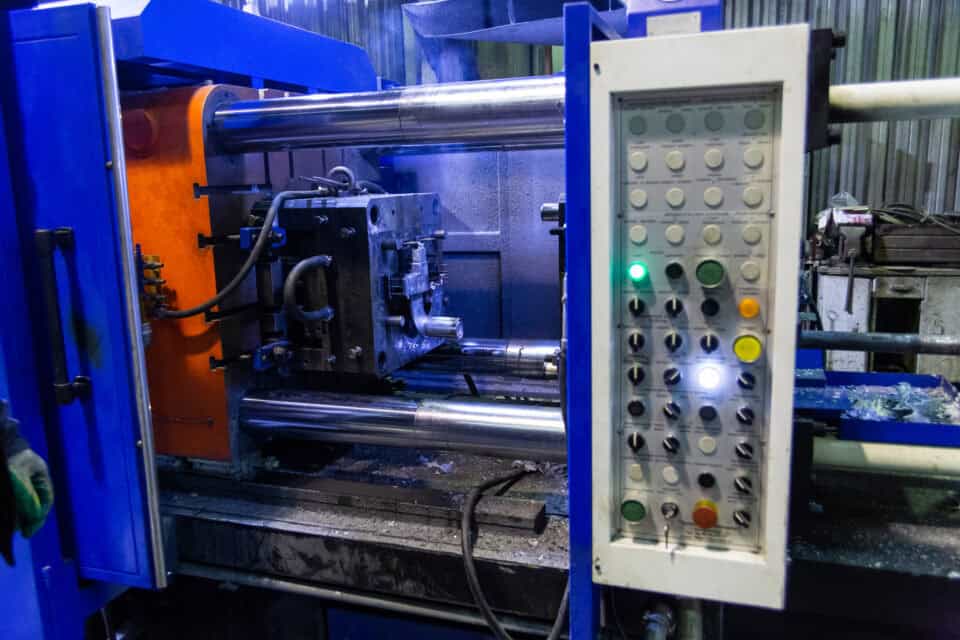
24h
Quick Quote±0.01
mm Tolerance20%
Purchase Cost Savings
Die Casting Process
Die casting is an advanced manufacturing technique that utilizes reusable metal dies to produce precise metal components with superior mechanical properties. Our expertise lies in designing durable dies tailored to each customer’s specifications, crafted from high-quality materials for extended use with minimal wear.
In the die casting process, certified alloys like zinc, aluminum, magnesium, or copper are melted to exact chemical specifications. The molten metal is injected into steel dies at high pressures, filling intricate cavities and rapidly cooling to form finely-grained solid parts.
With precision die casting machines ranging from 25 to 1,500 tons, we efficiently produce high-volume components at a lower cost compared to alternative methods, making it an ideal solution for complex parts in moderate to high production volumes.
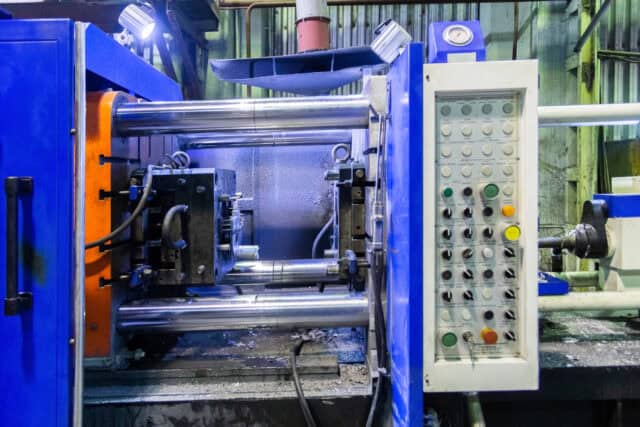
Service Features
Customized for Your Application
With a broad range of sizes from 10 oz to 75 lbs, we can produce small, intricate components as well large structural castings. Our machining and finishing capabilities include CNC operations to hit tight tolerances.
Range of Sizes and Geometries
We specialize in producing castings from 1 inch to 20 inches, with weights as low as 10 ounces all the way up to 20 Pounds. We can accommodate details with wall thicknesses down to 0.030 inch and tight tolerances of ±0.01 inch.
Quality Machining and Finishing
To ensure your cast components have critical features within tight dimensional tolerances, we offer comprehensive CNC machining capabilities as a secondary operation. Additional finishing processes like shot blasting, polishing, coating and plating can provide decorative, wear-resistant, or enhanced corrosion protection properties.
Rapid Turnaround Prototyping
We understand the need to get functional prototypes built quickly to test new designs. With in-house tooling and process know-how, we can quickly produce pre-production parts from your CAD models without the wait for hard tooling. When you are ready for full production, your proven tooling is ready to go.
Get in Touch with Our Experts
- Respond to the request within 2 hours
- 30 days to complete the mold
- Sample production in 7 days
All uploads are secure and confidential
Types of Die Casting Services We Offer
We offer a number of different die casting processes, including high pressure, low pressure, vacuum die casting, squeeze casting, semi-solid casting, gravity die casting and more.
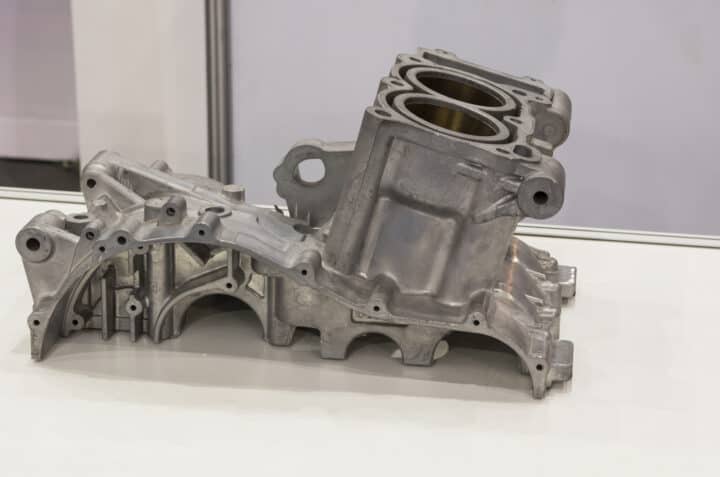
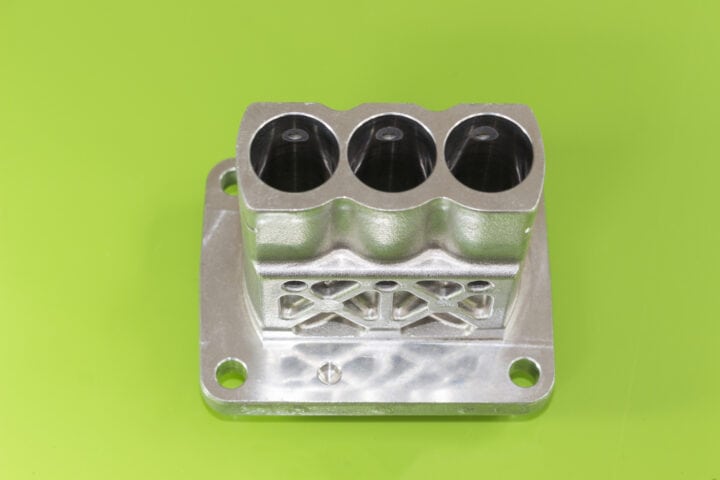
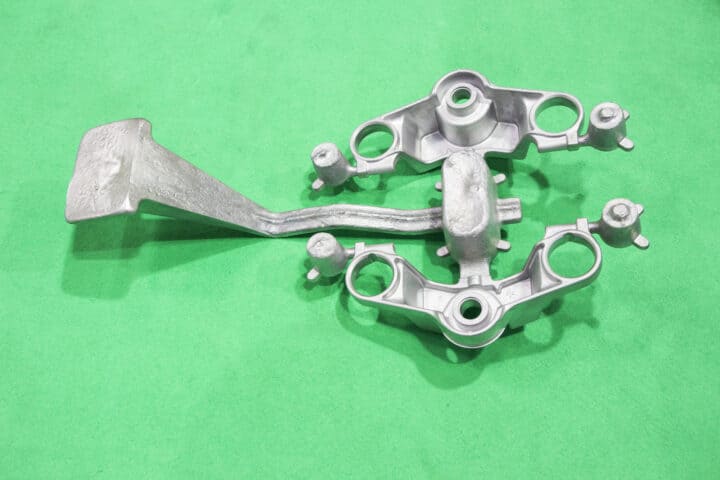
Broad Alloy Support for Diverse Applications
- Aluminum Alloys
- Zinc Alloys
- Magnesium Alloys
- Aluminum Alloys
- Zinc Alloys
Zinc Alloys
Learn MoreOur zinc pressure die casting alloys ne m Zamak d for decorative components to high
strength ZA-12 sed for small mechanical parts alo witht er resse and ar. Secondary plating improves corrosion and ric.
- Magnesium Alloys
- none
Enhanced Properties Through Secondary Processing
Surface Finish
Beyond the inherent properties of our certified die casting alloys, a variety of secondary processing and finishing operations can provide improved resistance to wear, corrosion, erosion, electrical conductivity, microwave transparency, and tailored aesthetic qualities.
Name | Description |
---|---|
As-Cast Finish | The as-cast condition directly out of the ceramic shell mold offers a cost-effective option when surface properties can be utilized as is. Minimal manual grinding/deburring provided. |
Abrasive Finishing | Uniform abrasive finishing like barrel tumbling or as-required spot grinding/linishing provided to offer enhanced flatness and improved cosmetic appearance. |
Polishing | Manual or automated buffing/polishing provided to obtain soft satin matte textures or brighter polished finishes - ranging from brushed to high gloss mirrors. Great for decorative components. |
Metallic Coatings | Functional metallic coatings including nickel, copper, zinc and precious metal plating provided to enhance corrosion resistance, electrical conductivity, solderability or other surface properties. |
Paint and Dry Film Coatings | Polymer coatings including powder coating, epoxy, polyurethane, silicone etc can be applied on investment castings to obtain thickness, chemical, wear and UV resistance properties. Aesthetic colors/effects. |
CNC Machining | Precision CNC milling, turning, drilling and other machining processes provided either for critical dimensions not achievable in casting or for enhanced surface finish requirements. Hole tolerances within 0.02mm demonstrated. |
Get a Free Instant Quote
We will respond quickly to your needs within two hours and instantly customize a solution for you based on the information and drawings you provide.
Get Free Quote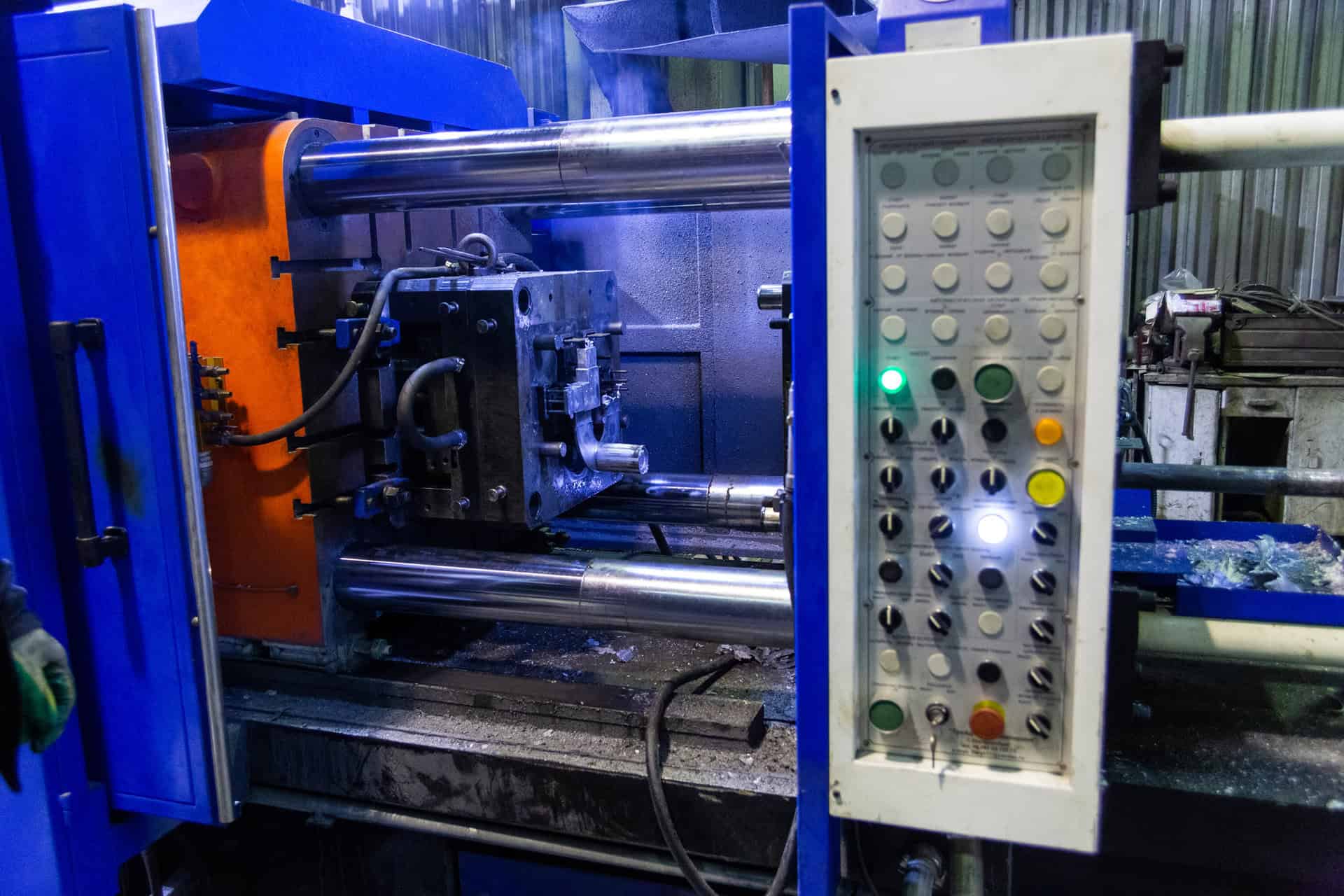
Applications
Innovation Across Industries
We drive innovation in aerospace, automotive, medical, and more through critical component development with our advanced die casting capabilities.
Die Casting Advantages and Disadvantages
Optimized Designs Extract Maximum Benefit
While die casting production has higher startup costs, it enables lightweight complex components in moderate to high volumes at a relatively low unit price.
Your Trusted Partner in Die Casting
Why Choose Us
With over 12+ years of die casting expertise, we deliver high quality, innovative solutions through strategic partnerships with our customers.
Innovative Solutions
Our expert engineering team combines hands-on design with cutting-edge simulation tools, optimizing quality, cost, and performance. With over 2000 unique designs, we stay at the forefront of innovation.
Customer Partnerships
As an extension of your team, we closely collaborate, understanding requirements, fostering open dialogue, refining processes swiftly, and ensuring satisfaction through shared success metrics and commitment.
Continuous Improvement
Embracing continuous improvement in people, processes, and technology, we perform 20+ quality checks, monitor 150K data points annually, and invest significantly in training/certification for lasting customer value.
Flexibility to Meet Demand
Our 15 die casting machines (25 to 1,500 tons) and flexible shifts seamlessly meet diverse customer demands. Strategic investments in automation and quality enhance capacity, maintaining short lead times.
Answers to Common Questions
We get asked a variety of questions about our die casting and machining services as well as how to get started on custom projects. Below we answer some of the most common queries we receive. If you have any other questions, please contact us!
What tolerances can you hold on die cast parts?
What level of surface finishes can be achieved?
Can you guarantee zero porosity in my die cast parts?
What design assistance does your team provide?
What lead time can I expect to receive prototypes?
How do I get started on a new project?
Get a Free Instant Quote Now
Contact Us Today
Our experts are online 24h, will respond quickly within two hours of receiving your demand, and immediately customize personalized one-stop solutions for you according to the information and drawings you provide.
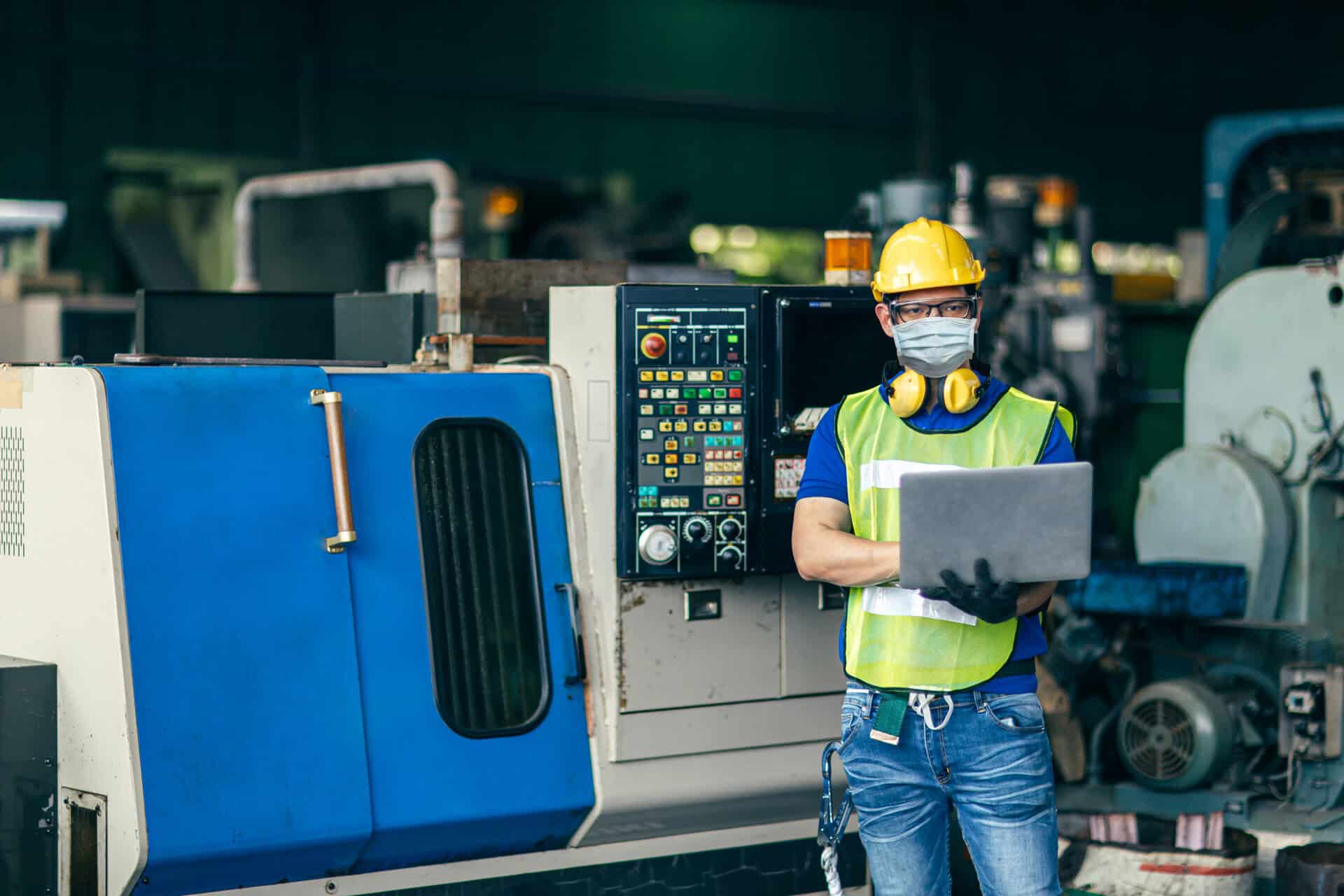